Piezoelectric ceramics are functional ceramic materials that can mutually convert mechanical energy and electrical energy. The so-called piezoelectric effect means that when some medium is subjected to mechanical pressure, even if the pressure is as small as sound wave vibration, it will produce shape changes such as compression or elongation, causing the surface of the medium to be charged. This is the positive piezoelectric effect. On the contrary, when an excitation electric field is applied, the medium will produce mechanical deformation, which is called the inverse piezoelectric effect. This wonderful effect has been applied in many fields closely related to people’s lives to realize functions such as energy conversion, sensing, driving, and frequency control.
In terms of energy conversion, the use of piezoelectric ceramics to convert mechanical energy into electrical energy can be used to manufacture piezoelectric igniters, mobile X-ray power supplies, and shell detonating devices. There are flints made of piezoelectric ceramics in electronic lighters, and the number of ignitions can be more than 1 million. Using piezoelectric ceramics to convert electrical energy into ultrasonic vibrations can be used to find the position and shape of underwater fish, non-destructive testing of metals, ultrasonic cleaning, ultrasonic medical treatment, and various ultrasonic cutters, welding devices and Soldering iron, processing plastic and even metal.
Click Here To See Piezo Ceramis Products
The manufacturing process of piezoelectric ceramics
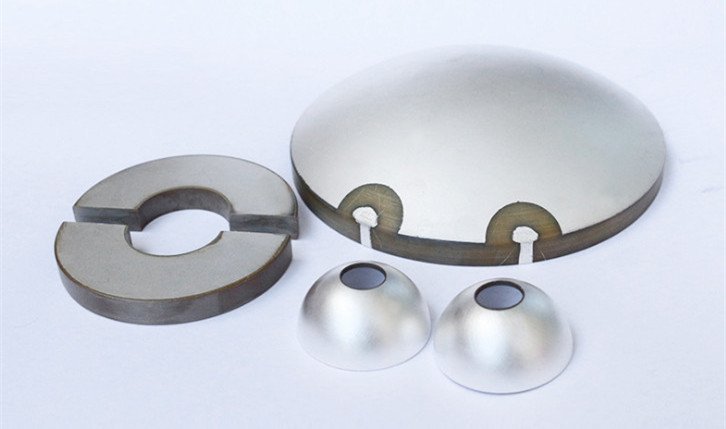
The general process flow of piezoelectric ceramics:
(1) Ingredients: Carry out pre-treatment of materials, remove impurities and damp, and then weigh various raw materials according to the formula ratio. Note that a small amount of additives should be placed in the middle of the bulk.
(2) Mixing and grinding: The purpose is to mix and grind various raw materials to prepare conditions for pre-burning for complete solid-phase reaction. Generally, dry grinding or wet grinding is adopted. Dry milling can be used for small batches, and agitating ball milling or jet pulverization can be used for large batches, with higher efficiency.
(3) Pre-sintering: The purpose is to synthesize piezoelectric ceramics by solid-phase reaction of each raw material at high temperature. This process is very important and will directly affect the sintering conditions and the performance of the final product.
(4) Secondary fine grinding: The purpose is to vibrate and grind the pre-fired piezoelectric ceramic powder finely, so as to lay a solid foundation for uniform ceramic formation and consistent performance.
(5) Granulation: The purpose is to make the powder form high-density particles with good fluidity. The method can be carried out manually but the efficiency is low. The current efficient method is to use spray granulation. Adhesives are added in this process.
(6) Forming: The purpose is to compact the pelletized material into a blank of the required prefabricated size.
(7) Plastic ejection: the purpose is to remove the binder added during granulation from the blank.
(8) Sintering into porcelain: the blank is sealed and sintered into porcelain at high temperature. This link is very important.
(9) Shape processing: Grind and process the burned products to the required finished size.
(10) Electrode: set a conductive electrode on the required ceramic surface. The general methods include silver layer burning infiltration, chemical deposition and vacuum coating.
(II) High voltage polarization: Orientation of the electrical domains inside the ceramic, so that the ceramic has piezoelectric properties.
(12) Aging test: After the ceramic performance is stable, various indicators are tested to see if the expected performance requirements are met.
Hi, This is very interesting,
I am studying it.